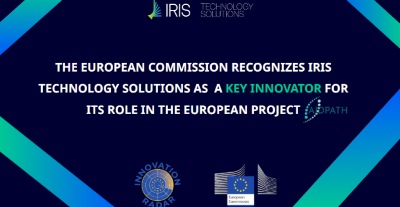
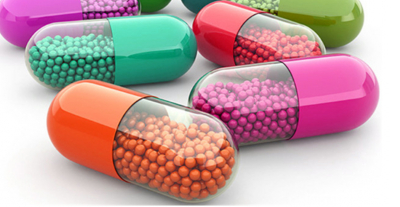
Monitorização dos processos de mistura por espetroscopia NIR em linha e em tempo real
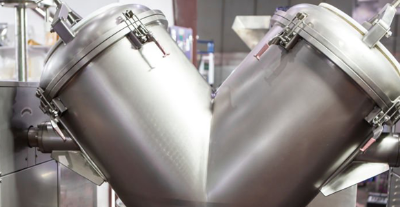
Monitorização dos processos de mistura por espetroscopia NIR em linha e em tempo real
O processo de mistura de pós é o processo mais popular para obter uniformidade de conteúdo em formas sólidas. Apesar da sua aparente simplicidade, ou seja, tirar partido das forças de cisalhamento para misturar IFAs e excipientes movendo simplesmente o recipiente durante algum tempo, qualquer especialista em galénica sabe que o comportamento real da mistura não é assim tão simples. De facto, a distribuição final resulta de uma combinação caótica de interacções microscópicas das partículas e da mecânica de fluxo macroscópica, para não mencionar que, uma vez atingida a homogeneidade, existe um risco real de não mistura como consequência da afinidade entre partículas homólogas. Por conseguinte, independentemente das melhorias mecânicas na conceção do misturador, a verificação sistemática da homogeneidade da mistura é um requisito fundamental no sector farmacêutico e nutracêutico. Daí a importância de monitorização dos processos de mistura por espetroscopia NIR em tempo real.
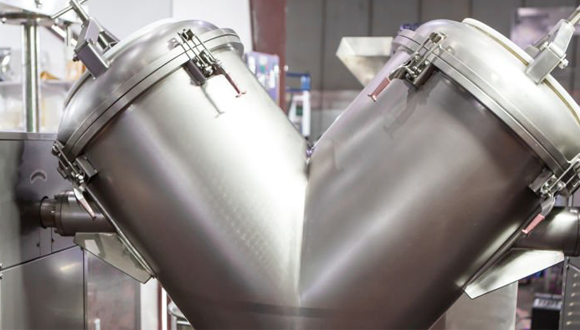
Controlo tradicional vs. monitorização dos processos de mistura por espetroscopia NIR
Até agora, a forma tradicional de o fazer tem sido parar periodicamente o processo de mistura após vários ciclos (tempos) para recolher algumas amostras de diferentes pontos, que são subsequentemente analisadas por cromatografia. No entanto, esta abordagem também tem alguns inconvenientes indesejáveis, como o aumento do tempo de espera (devido aos procedimentos laboratoriais complicados envolvidos), o tempo de mistura sub-ótimo (devido à mistura prolongada arbitrária para garantir a homogeneidade) e os artefactos de mistura (como a não mistura e a formação de grumos como consequência da manutenção da carga em condições estáticas enquanto se aguardam os resultados laboratoriais).
Em contrapartida, uma abordagem PAT, como a monitorização do processos de mistura em tempo real com base na espetroscopia NIR, pode ser considerada a melhor forma de verificar se a condição do ponto final foi atingida. De facto, tanto a FDA como a EMA descreveram esta abordagem como um novo paradigma recomendado para o controlo dos processos de mistura de pós.
Em princípio, tal como descrito em pormenor na literatura científica, existem duas formas de implementar uma determinação do ponto final baseada em PAT: utilizando um modelo preditivo de machine learning supervisionado (por exemplo, um modelo PLS que prevê quantitativamente a concentração de API) ou utilizando um algoritmo de monitorização do processo de mistura agnóstico à composição específica da mistura. O primeiro produz normalmente resultados mais directos e precisos, mas requer, por sua vez, o desenvolvimento de modelos específicos a partir de amostras de referência adequadas, o que nem sempre é viável, especialmente quando existem muitas formulações e misturas diferentes. A abordagem agnóstica para monitorização dos processos de mistura, por outro lado, baseia-se na semelhança espetral; não são necessários previamente dados reais sobre a composição específica da formulação.
A abordagem agnóstica: Desvio-padrão de bloco móvel (MBSD) e o algoritmo dinâmico da IRIS Technology Solutions
De facto, a estabilidade espetral é agnóstica em relação à composição específica de cada formulação. Não há necessidade de desenvolver qualquer modelo de previsão quantitativa para avaliar as concentrações dos componentes porque o raciocínio subjacente afirma que, independentemente da composição, a homogeneidade não pode ser melhorada quando os espectros permanecem inalterados, pelo menos para os componentes principais. De facto, uma mistura pode ser considerada homogénea quando os seus espectros permanecem inalterados após vários ciclos de mistura.
Uma vez que a espetroscopia NIR é sensível a concentrações de 0,1-1 % ou superiores, a homogeneidade dos componentes minoritários não pode ser avaliada por espetroscopia NIR. No entanto, pode ser inferida a partir da homogeneidade dos componentes principais ou maioritários e validada oportunamente com métodos laboratoriais tradicionais, se necessário.
O desvio-padrão do bloco móvel (MBSD) é o algoritmo agnóstico mais amplamente descrito, pelo menos na literatura científica, e utilizado pela maioria dos fabricantes de analisadores NIR. Normalmente, o critério do ponto final do MBSD é bastante arbitrário. Mesmo quando é utilizado um critério baseado em estatísticas [Avaliação crítica de métodos para a determinação do ponto final em processos de mistura farmacêutica. M. Blanco, R. Cueva-Mestanza e J. Cruz. Anal. Methods, 2012, 4, 2694], é necessário cumprir algum pressuposto restritivo sobre a distribuição da métrica de semelhança para que esta seja corretamente aplicável. Além disso, o desvio-padrão médio tem um efeito de “suavização” que pode ocultar, em certa medida, a verdadeira tendência da semelhança espetral.
A abordagem dinâmica para monitorizar processos de mistura com Visum NIR In-Line™.
O algoritmo patenteado da IRIS Technology Solutions para a monitorização e otimização do processo de mistura, por outro lado, baseia-se no teste da estabilidade de uma métrica de semelhança real (MSD: diferença média quadrada entre dois espectros sucessivos) utilizando critérios estatísticos fortes na distribuição MSD específica da mistura. Com efeito, a nossa abordagem de blocos móveis adapta dinamicamente o limiar a cada distribuição estatística da semelhança espetral em função da formulação. Consequentemente, fornece um critério de ponto final robusto para Monitorização dos processos de mistura independentemente do comportamento específico da formulação, o que é particularmente necessário quando ocorrem anomalias de mistura como a não mistura, segregação ou aglomeração.
Por uma questão de flexibilidade, os utilizadores podem ajustar o tamanho do bloco móvel e a significância estatística de acordo com a sua conveniência. Sempre que possível, estes parâmetros devem ser ajustados na fase de arranque do sistema de análise do processo de mistura, embora as predefinições de fábrica funcionem para a maioria das aplicações ou circunstâncias.
Figura 1: Módulo adaptador de janela de safira para o analisador Visum NIR In-Line ™ fabricado pela IRIS Technology Solutions S.L.
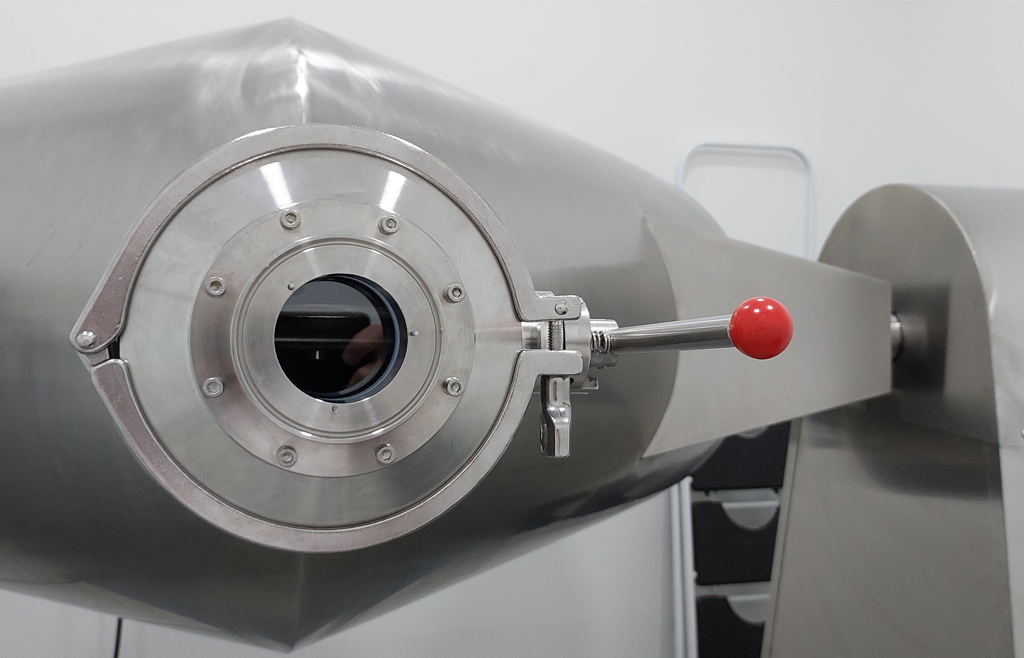
O módulo adaptador com janela de safira permite uma fácil integração do analisador Visum NIR In-Line™ através de uma ligação de tripla fixação. Estão disponíveis diferentes tamanhos do módulo adaptador, consoante as configurações próprias do misturador.
Ao contrário de outros analisadores no mercado, o Visum NIR In-Line™ é um analisador autónomo e pode comunicar com vários protocolos de comunicação. Também cumpre os regulamentos farmacêuticos 21 CFR Parte 11 (FDA), os requisitos da Farmacopeia Americana (USP) e da Farmacopeia Europeia (Ph. Eur.) e as Directrizes da Agência Europeia de Medicamentos (EMA) de 2014 e 2023.
Na sua versão Blender, o analisador Visum NIR In-Line™ é sem fios, alimentado por baterias recarregáveis e substituíveis com uma autonomia de mais de 3 horas e ligado através de Wi-Fi, como mostra a imagem abaixo.
Figura 2: Analisador Visum NIR In-Line™ monitorização dos processos de mistura.
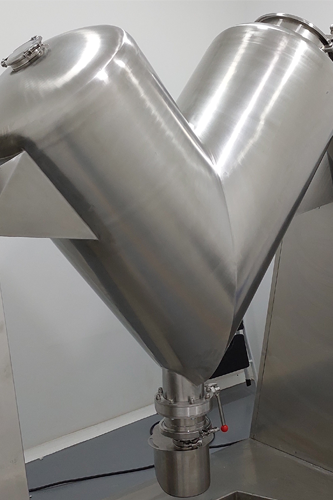
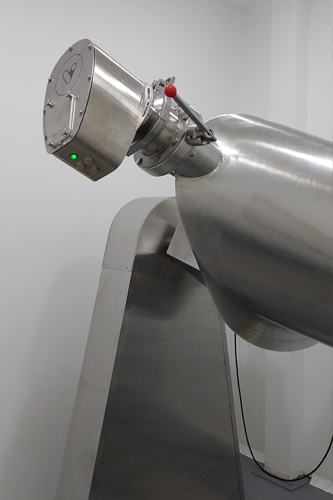
Tabela 1: Especificações técnicas do analisador em linha Visum NIR In-Line™
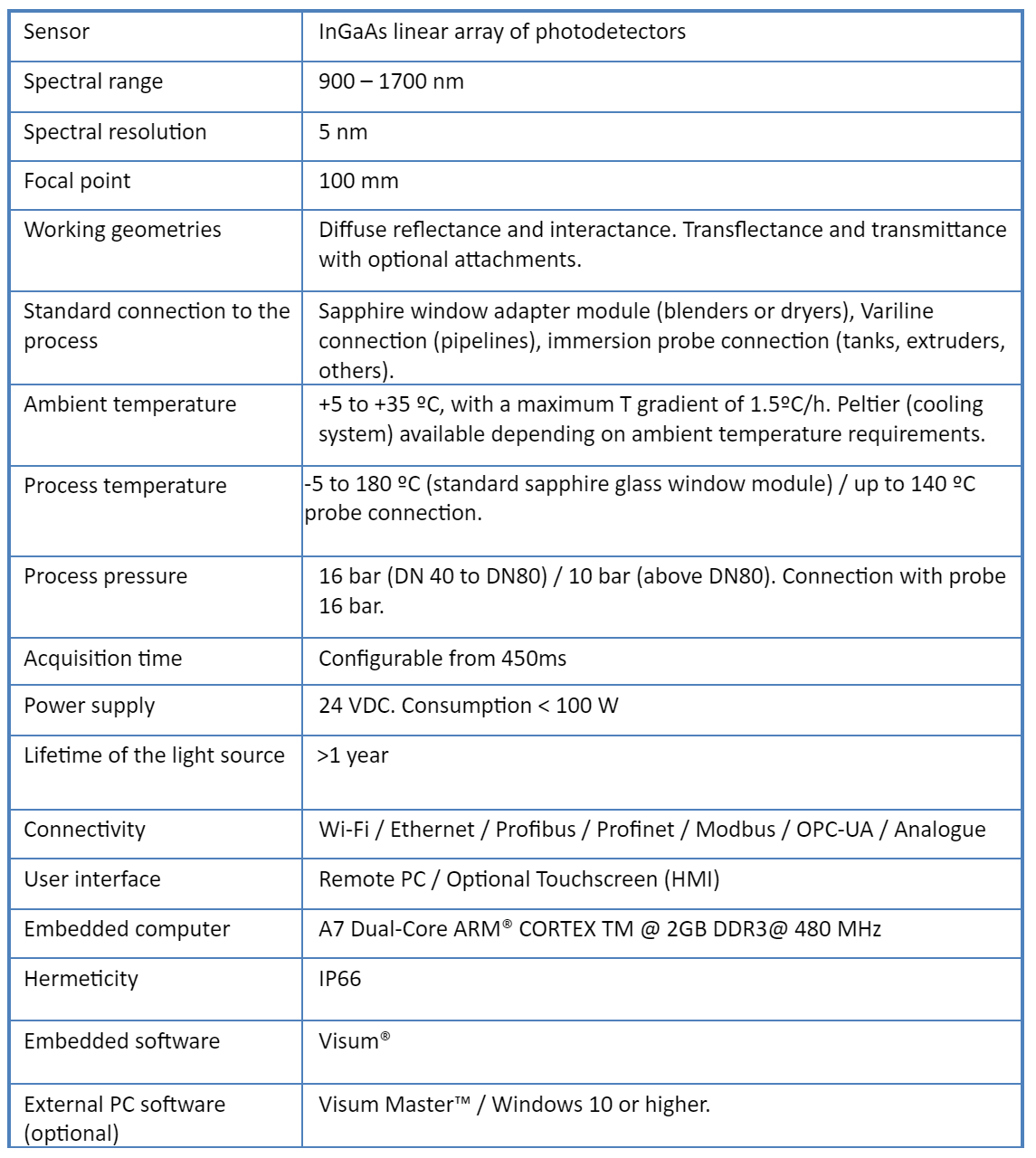
Conclusões
O analisador Visum NIR In-Line™ da IRIS Technology Solutions S.L. apresenta um método dinâmico mais robusto e realista de monitorização de processos de mistura do que o algoritmo de desvio padrão de bloco móvel (MBSD) baseado na média quadrática de dois espectros sucessivos e não na média do desvio padrão como índice de semelhança utilizado pela abordagem MBSD.
Como tem um computador incorporado, não precisa de ser ligado a outros dispositivos electrónicos ou computadores externos, o que o torna uma excelente ferramenta autónoma para trabalhar ao nível da produção da fábrica e em ambientes GMP.