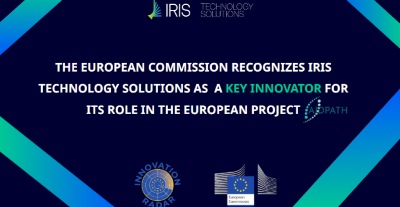
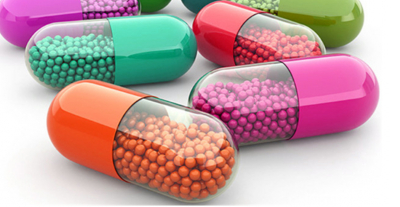
Blending process monitoring with in-line NIR spectroscopy
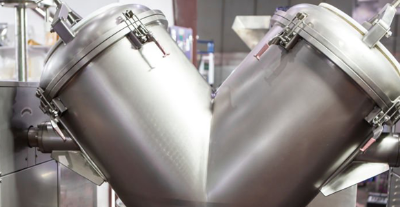
Real-Time blending process monitoring with NIR spectroscopy
Powders blending process is the most popular to achieve content uniformity in solid forms. Despite its apparent simplicity, i.e., taking advantage of shear forces for mixing APIs and excipients by merely moving the container for a certain time, any specialist in galenic does know that the real behavior of the mixture is not that simple. In fact, the final distribution results from a chaotic combination of microscopic interactions among the particles and macroscopic flow mechanics, not to mention that, once the homogeneity has been achieved, there is a real risk of demixing as a consequence of the affinity among homologous particles. That is why, regardless of the mechanical improvements in the blender’s design, systematically checking for mixture homogeneity is a key requirement in the pharmaceutical and nutraceutical sector. This is where NIR becomes important as a technique for real-time blending process monitoring.
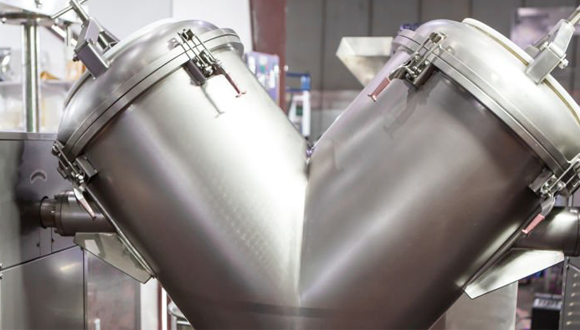
Traditional control of the blending process vs. Blending process monitoring (PAT)
Up to now, periodically stopping the blending process after several cycles in order to take some samples from different points, which are further analysed by chromatography, has been the traditional way to do it. However, such an approach has also certain unwanted drawbacks, namely added lead time (due to the involved cumbersome lab procedures), suboptimal blending time (because of arbitrary extended blending intended for guaranteeing homogeneity) and blending artifacts (such as demixing and lumps as a consequence of keeping the load in static conditions while waiting for the lab results).
On the contrary, a PAT approach, such as a spectroscopy-based real time blending process monitoring, could be deemed the optimal way to check if the endpoint condition has been reached. In fact, both FDA and EMA have described such an approach as a recommended new paradigm.
In principle, as thoroughly described in the scientific literature, there are two ways for implementing a PAT-based endpoint determination: by using a supervised machine learning predictive model (for example, a PLS model that quantitatively predicts the API concentration) or by using an algorithm agnostic to the specific composition of the mixture. The first one usually renders more direct and accurate results but, in turn, it requires developing specific models on the basis of suitable reference samples, which is not always feasible, especially when there are too many different formulations. The agnostic approach for blending process monitoring, on the contrary, is based on spectral similarity; no ground truth data on the specific composition of each formulation is required in advance.
The agnostic approach: Moving-block Standard Deviation and the dynamic algorithm by IRIS Technology Solutions
Spectral stability is, in fact, agnostic to the specific composition of each formulation. No quantitative predictive model has to be developed for assessing the components concentrations because the underlying rationale states that, regardless of the composition, no improvement in homogeneity can be made once the spectra remain unchanged, at least for the major components. Indeed, a mixture can be deemed homogeneous once their spectra remain unchanged after several blending cycles.
Since the NIR spectroscopy is sensitive to 0.1-1 % or higher concentrations, during during blending process monitoring the homogeneity of minor components cannot be assessed by means of such a technology. However, it can be inferred from the homogeneity of major components and opportunely validated with traditional lab methods if required.
Moving-block Standard Deviation (MBSD) is the most widely described agnostic algorithm, at least in the scientific literature. Usually, the MBSD endpoint criterion is rather arbitrary. Even when a statistically-founded criterion is used [Critical evaluation of methods for end-point determination in pharmaceutical blending processes. M. Blanco, R. Cueva-Mestanza and J. Cruz. Anal. Methods, 2012, 4, 2694], some restrictive hypothesis on the distribution of the similarity metric should be fulfilled in order to be properly applicable. Moreover, the mean of the standard deviation has a rather “smoothing” effect that could veil to some extent the real trend of the spectral similarity.
The dynamic approach with Visum NIR In-Line™ for blending process monitoring
IRIS Technology Solutions’ proprietary algorithm, on the contrary, is based on checking for the stability of a true similarity metric (MSD: mean squared difference between two successive spectra) by using strong statistical criteria on the blending-specific MSD distribution. In fact, our moving block approach dynamically adapts the threshold to each formulation-wise spectral-similarity statistical distribution. Consequently, it provides a robust endpoint criterion for blending process monitoring regardless of the specific behavior of each formulation, which is particularly required when mixing anomalies such as demixing or lumps formation take place.
For the sake of flexibility, the users can set both the moving block size and the statistical significance at their convenience. Whenever possible, such parameters should be tuned in the commissioning stage although the factory-set values should work for the most frequent circumstances.
Image 1: Sapphire window adapter module for Visum NIR In-Line analyser ™ manufactured by IRIS Technology Solutions S.L.
The adapter module with sapphire window allows easy integration of the Visum NIR In-Line™ analyser via a tri clamp connection. There are different sizes of the adapter module depending on the blending machine’s own configurations.
Unlike other analysers on the market, the Visum NIR In-Line™ is a self-contained analyser (embedded computer) and can communicate with multiple communication protocols. It also complies with the pharmaceutical regulation 21 CFR Part 11 (FDA), the requirements of the American (USP) and European (Ph. Eur.) Pharmacopoeia and the European Medicines Agency (EMA) Guidelines 2014 and 2023.
In its Blender version, the Visum NIR In-Line™ analyser is wireless, powered by rechargeable and replaceable batteries with a battery life of more than 3 hours and connected via Wi-Fi, as shown in the image below.
Image 2: Visum NIR In-Line™ analyser in a blending process monitoring cycle.
Table 1: Visum NIR In-Line analyser ™ technical specifications
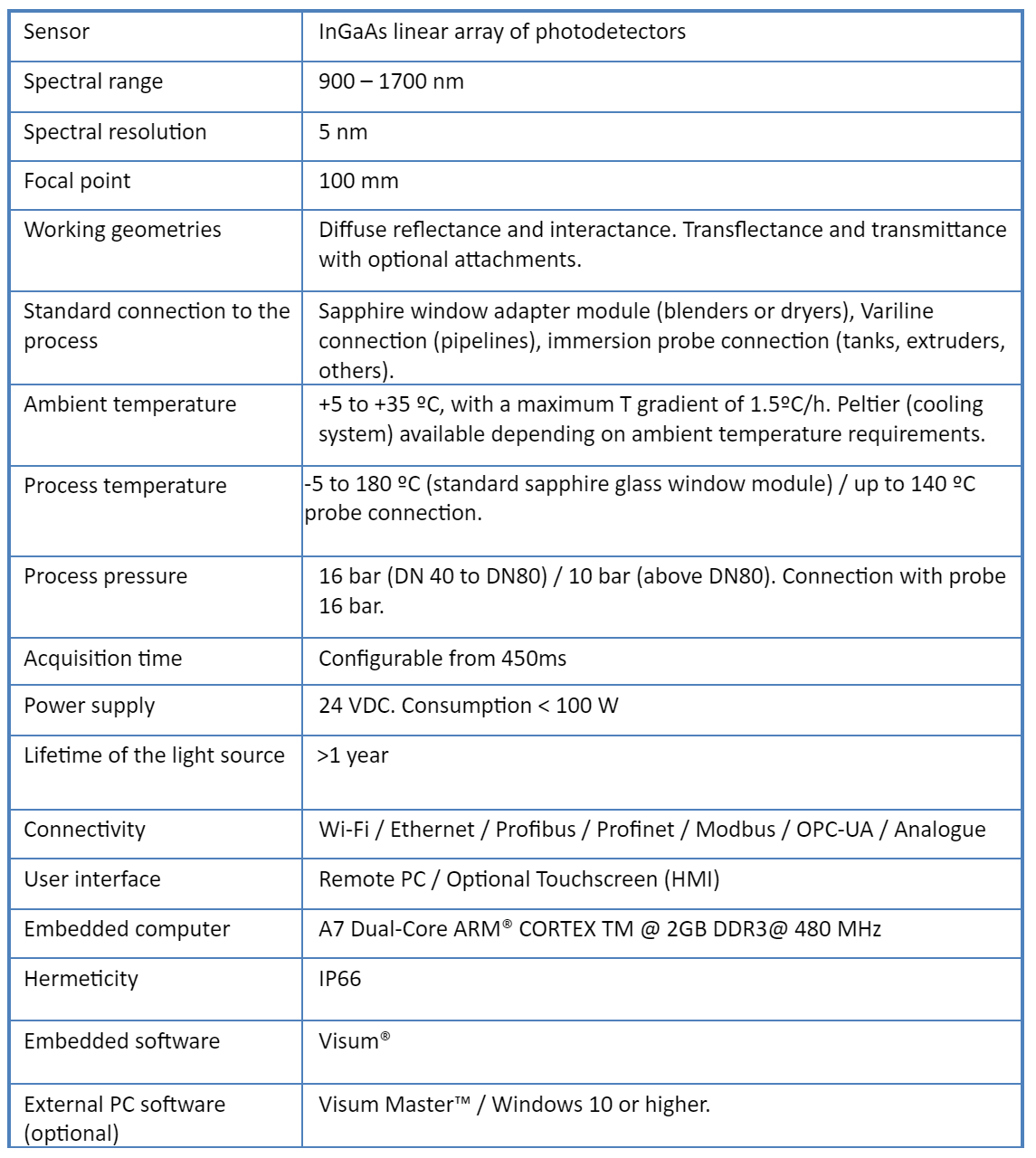
Conclusions
The IRIS Technology Solutions S.L. In-Line™ NIR analyser presents a more robust and realistic dynamic method for blending process monitoring than the Moving-block Standard Deviation (MBSD) algorithm in that it is based on the quadratic mean of two successive spectra and not on the average of the standard deviation as a similarity index used by the MBSD approach.
As it has an embedded computer, it does not need to be connected to other electronic devices or external computers, making it an excellent stand-alone tool for working at the plant production level and in GMP environments.
In addition, it has a much larger illumination and spectrum acquisition area than other NIR analysers, especially those very small ones, with a resolution of 256 pixels, obtaining more chemical information and spectral quality for optimal monitoring of each blending cycle.